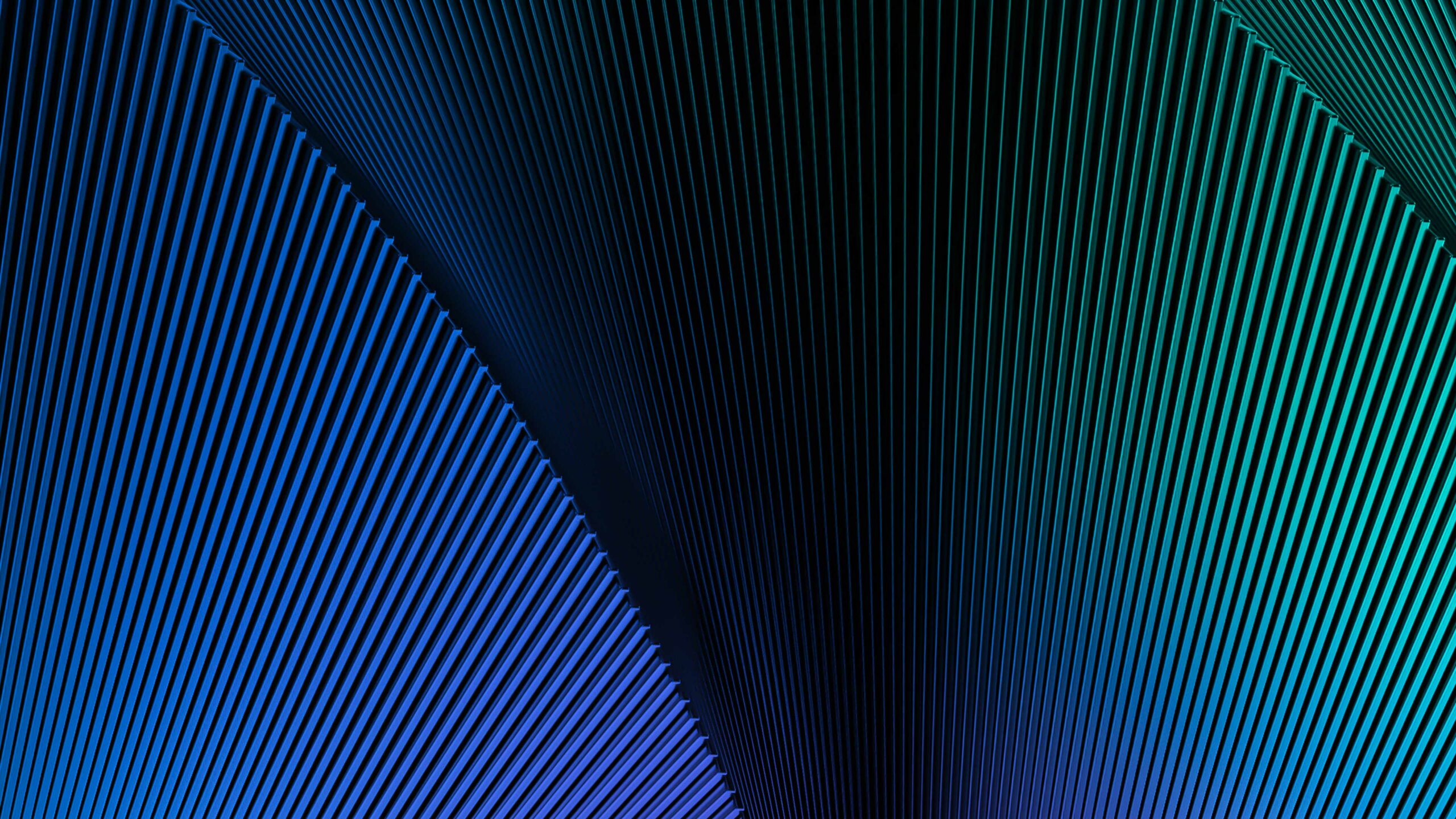
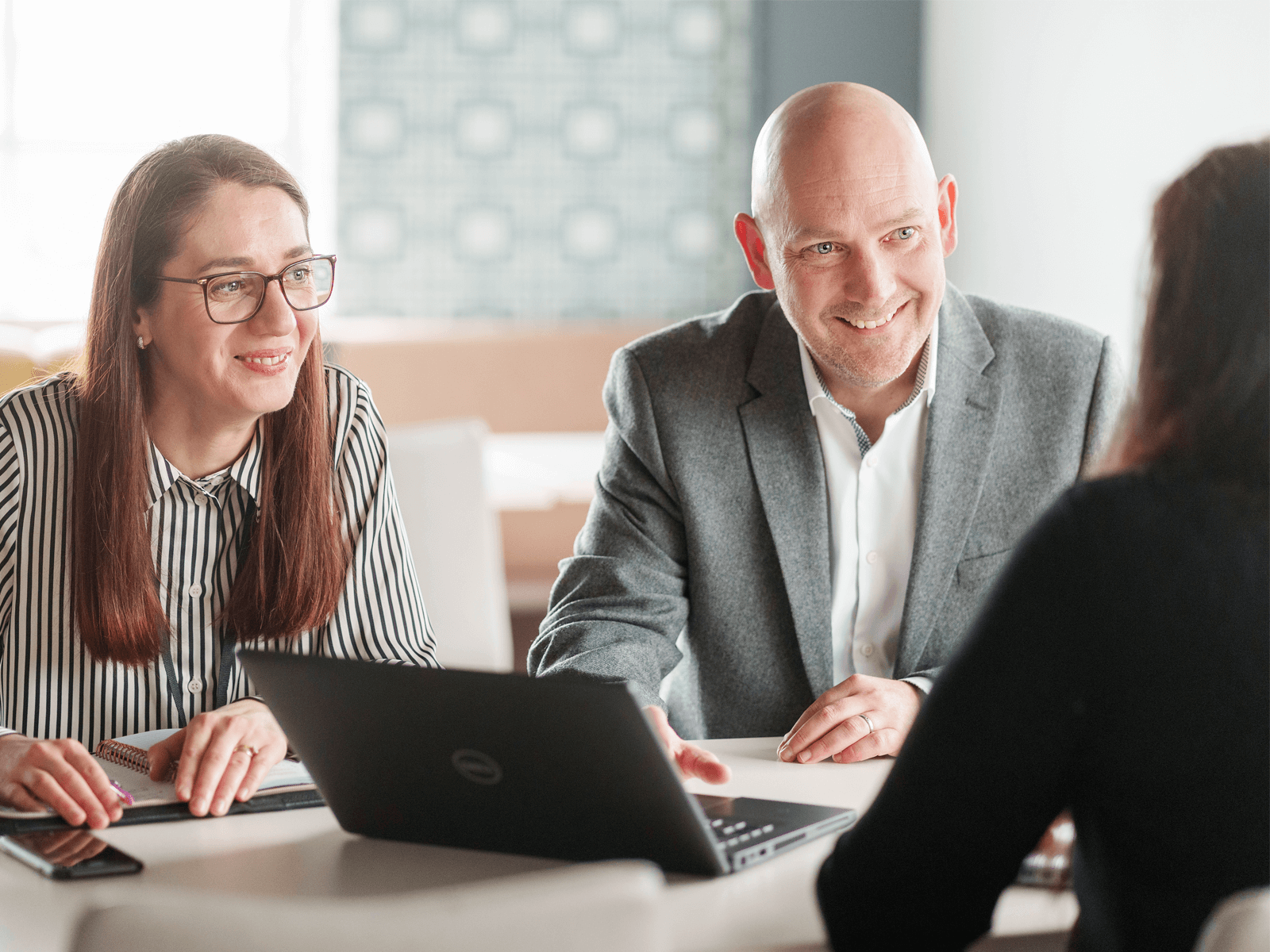
404 Page not found
Sorry, it looks like the page that you are looking for is no longer available on our new website, It may have been moved or deleted.
Sorry, it looks like the page that you are looking for is no longer available on our new website, It may have been moved or deleted.